Nowadays, with just two or three heavy snowfalls, ski resorts can maintain their slopes in good condition throughout the season thanks to this technological miracle. Let's see how it's done.
First, we should note that "artificial" snow is real snow, without any chemical ingredients - the only difference is that it's produced by machines, which is why in recent years there's been a tendency to call it "manufactured snow". Snowflakes are simply ice crystals. Naturally, water evaporates from rivers, seas and lakes. This moisture in the atmosphere, when certain air saturation conditions occur, falls back to earth as rain or, if it's cold enough, as snow. During their descent, the original crystals absorb more water, creating the famous structures we all recognise.
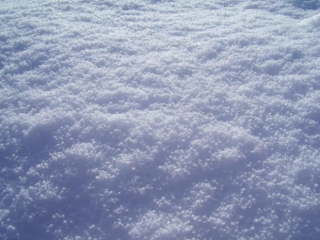
The machines essentially shorten this process. There's no evaporation phase; instead, water is pumped from a reservoir, lake or river to the famous snow cannons. There, it meets pressurised air that sprays it outward. The prevailing cold then does the rest, freezing these tiny water droplets before they reach the ground. The result: snow. Although if we examined it under a microscope, we'd find irregular pellets rather than the structure described earlier, mainly due to the speed of the process.
But not all manufactured snow is the same. In fact, it can be adjusted to our desires and needs. The first decision is determining the water quantity. While dry snow, with less water, is usually better for skiing due to its sliding characteristics, sometimes wetter snow is more desirable. The main reason is greater volume, allowing faster coverage of areas heavily eroded by skiers. Or at the start of the season, to create a good base, later adding dry snow on top. Maintaining slopes in good condition requires sufficiently cold temperatures and proper work with snow grooming machines.
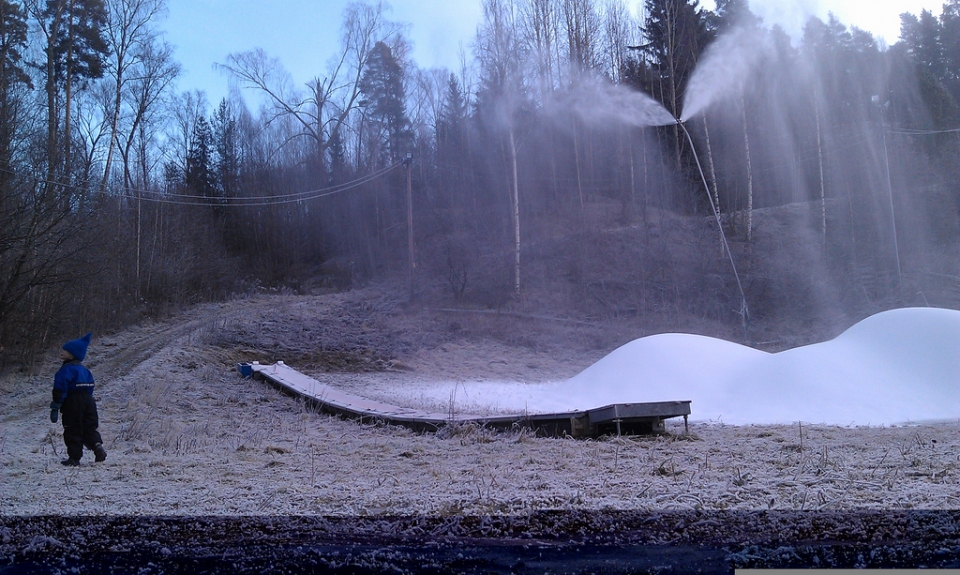
The second important factor is snow production frequency. Simply put, "fresh" snow is much more fun and easier to ski on. The ideal approach would be to produce a large volume of very heavy snow at season start to create a solid base, then produce drier, lighter snow as frequently as the local weather permits.
- Water
The starting point. While it might seem impressive that many resorts have cannons covering over 80% of their skiable area, what's more important is the amount of snow they can produce in a given time, indicating their capacity to open sooner or cover specific areas with fresh snow throughout the season. This all depends on the available water quantity and the pumping capacity of their facilities.
But once this water is available, what must we do? What makes it turn into snow? The water must be cooled before pumping to the cannons. In purely physical terms, cold doesn't exist; rather, there's heat transfer from higher to lower temperature bodies. When water freezes, it releases heat until completely crystallised. It's assumed that this occurs at 0°C, but in reality this only applies under very specific conditions (distilled water, 1 atm pressure).
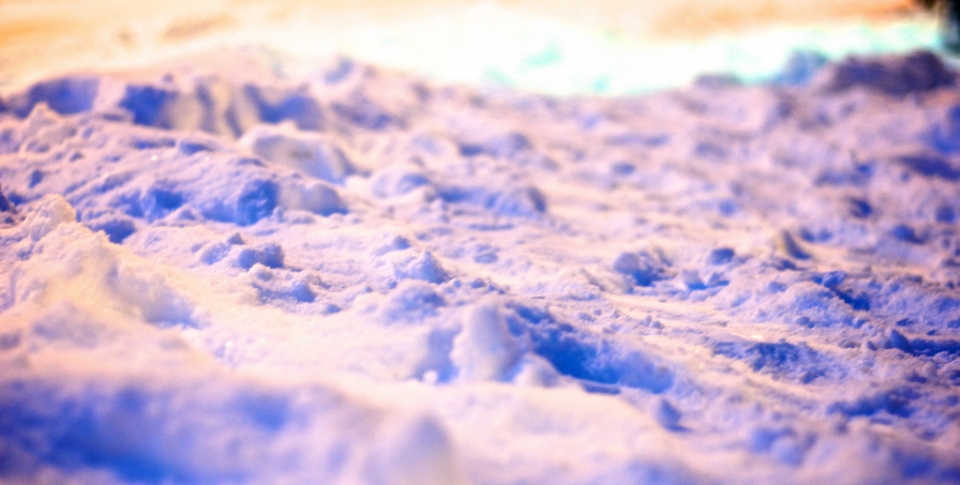
When we look at a thermometer, we're seeing the "dry" temperature. Knowing this might suffice for deciding whether to wear a coat, but not for snow production. We must know the ambient humidity.
To use a human body example: at 25°C with 95% relative humidity, we feel hot, and our body reacts by sweating. This sweat evaporates, but on a humid day, the air can't absorb as much as on a drier day - for example, at 30 degrees and 20% humidity, we lose heat faster, so it feels less hot despite the higher temperature.
The snow production process is similarly affected. When humidity is 100% (saturated air), wet and dry temperatures coincide at what's called the dew point. But when water content is low, even if traditional thermometers show above 0°, snow can still form due to the atmosphere's high moisture absorption capacity, easily freezing the cannon-sprayed droplets. The limit is typically around 4°C for very low relative humidity.
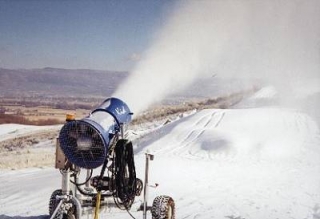
- Air
The key to making it all work. Air serves a dual purpose in snow production. Firstly, it "breaks up" the water into appropriately sized particles for freezing, propelling them outward. Secondly, the same air stream initiates the freezing process. Let's see how.
First, we must understand what happens during compression. Air is a gas, more specifically, a gas mixture. Unlike liquids, it can be compressed, meaning the same air volume can occupy much less space, albeit with consequent pressure increase. Gas laws establish relationships between pressure, volume and temperature, showing that increasing pressure raises temperature. But this temperature doesn't necessarily stay high - it can be reduced.
When compressed gas expands, the process reverses. Considerable mechanical energy is released while heat is absorbed. This is why air matters so much. The mechanical energy breaks water into small particles, while the heat absorption cools the water.
There are two variables for measuring a snow production system's capacity regarding air. One is the compressed volume, measured in cubic metres per minute entering compressors. The other is the pressure at which air is compressed.
The compression occurs in multiple serially arranged chambers with turbines between them. It's typically done in two or three stages, depending on desired final pressure (from atmospheric pressure (1atm) to 2, 5 and 10 successively).
Though most production systems work at 5atm, increasing pressure provides more mechanical energy, enabling snow production at higher ambient temperatures as the air stream delivers more cold. Additionally, if compressors allow, production can occur at lower pressure by connecting more cannons simultaneously.
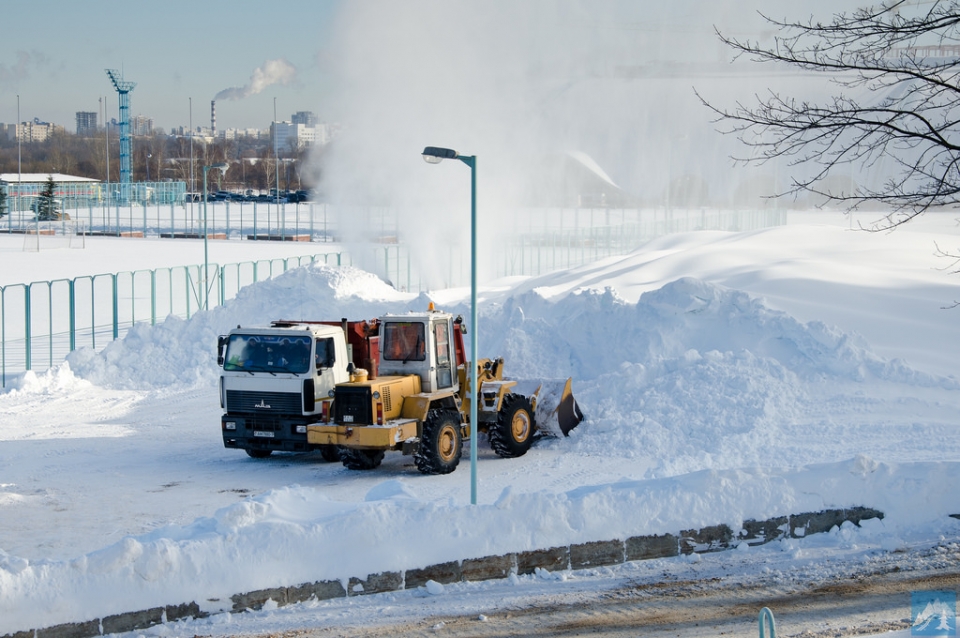
Compressing so much air at such pressure is expensive, so companies try to use every last cubic metre. For perspective, a compressor with installation can cost up to £300,000, and a resort might spend £1.2 million annually on fuel, maintenance and staff.
As mentioned, compressing air rapidly increases temperature. Early stages use water circulation for cooling. But in final stages, compression becomes so abrupt that temperatures reach 110°C. Leaving air like this would mean expansion cooling wouldn't freeze water, necessitating a refrigeration process in machines called aftercoolers.
There's another important reason for this process. Air also contains humidity (non-compressible), sometimes significantly. When this enters pipes leading to cannons, it gradually condenses, reducing pipe effective diameter and creating harmful pressure spikes or even blockages.
But most damaging is that less air reaches cannons, meaning less propulsion and cooling. The result is very wet snow or icy slopes. Aftercoolers lower temperature to condense humidity, removing it as pure water.
This entire air system has one purpose: creating the most homogeneous snow possible. With poor compression, differences emerge between upper and lower slope cannons, even between adjacent ones. Well-maintained equipment with sufficient capacity produces more, better-quality snow without significantly increasing costs.
- Cannons
Simply put, snow cannons are just pipes where water and air meet. The former is the raw material for snow, while the latter propels and cools the process. Simple, right? Manufacturers wish it were.
There are two main cannon types: airless models (called low-pressure in Spain) and air/water or high-pressure models.
Low-pressure cannons:
These can be permanent or mobile. They only need a water source and power supply. Shaped like barrels with water nozzles around the edge (similar to garden sprinklers), they have a central fan that further breaks up water droplets and propels them outward.
These cannons are cheaper than high-pressure models, mainly because no air compression or delivery is needed - just a high-voltage line by the slope. But they have drawbacks. Though producing large snow quantities, they're hard to move and typically cost over £12,000 per unit, excluding installation.
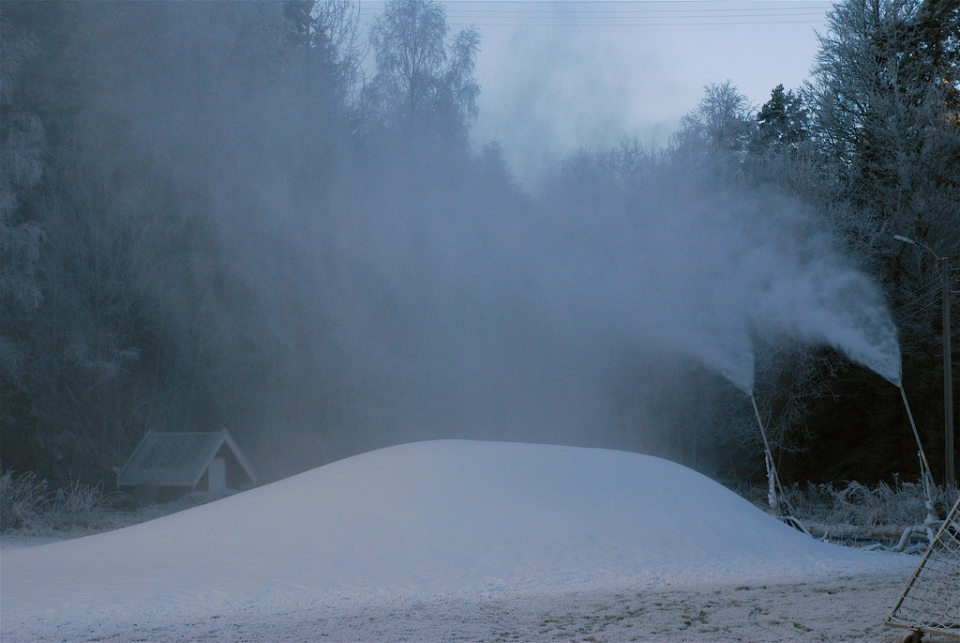
High-pressure cannons:
These are most commonly used at resorts, with over a dozen different models available. Early models were ingenious but inefficient, only producing good snow at very low temperatures. When popularised in the mid-70s, they improved significantly but still lagged far behind modern versions in ease of use, efficiency and production consistency.
Costing between £360 and £1,800, they remain expensive products. Price variations reflect different models' production volumes or optimal operating temperatures. Most resorts use older equipment, replacing it with new units when broken or expanding areas.
The perfect cannon should be simple, freeze-resistant, and project snow far to cover large areas. It should perform well across wide temperature ranges, producing uniformly sized snow while being energy-efficient (needing little compressed air, making it quieter). It should also be compact, lightweight and easy for staff to move when needed.
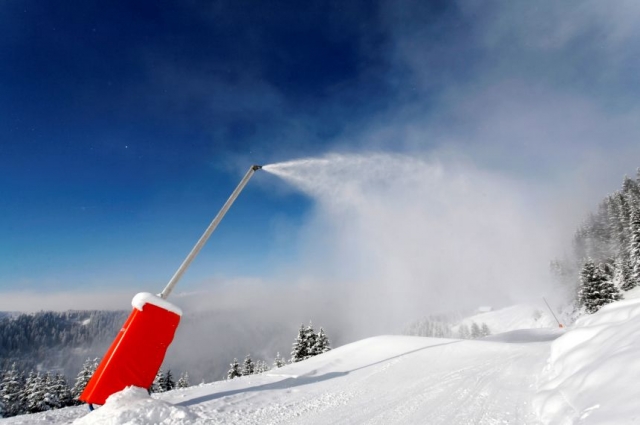
- Computers
They provide centralised control of pumps and compressors, ensuring production quality by adjusting for variable weather conditions.
Energy costs are managed several ways. First, operators know electricity usage in real-time, ensuring they don't exceed grid contracts. Second, they know which equipment is running and how, including water quantities being pumped at what pressure, plus available compressed air.
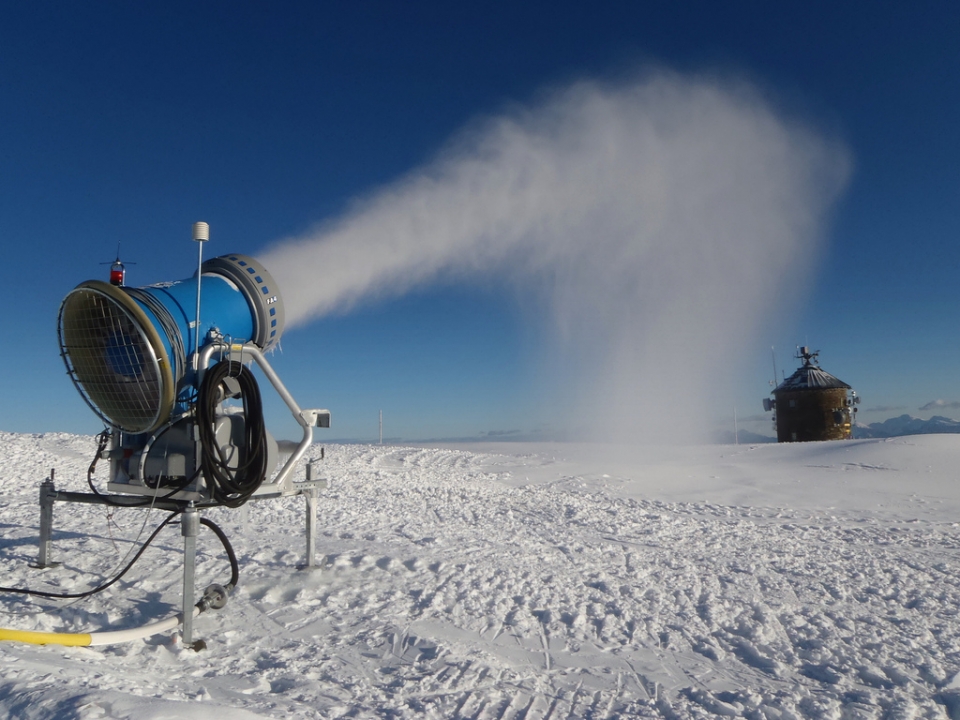
With this knowledge, controllers can start/stop compressors and pumps with a click, adding them to the system only when needed rather than wasting energy on excess connected capacity.
One of the biggest challenges in high-quality snow production is precisely controlling water per cubic metre of snow - the most critical parameter for weight and skiability. Until now, this required staff at each cannon adjusting mixtures based on experience.
This approach is highly subjective with much variability. Computers now recalculate all parameters per cannon using small weather stations across the mountain. Snow production still requires hard slope work, but these computerised systems eliminate much guesswork about water/air ratios, producing more homogeneous, higher-quality snow.
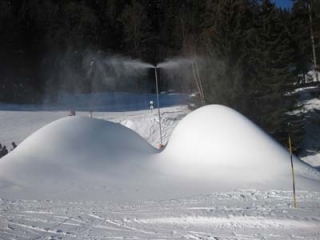
One frequent question about snow production concerns its environmental impact. First, remember no chemicals are used - just water. Does this water harm the environment?
Considering a medium-sized facility uses about 35,000 litres per minute, that seems like a lot of water. This produces roughly 85 cubic metres of snow - enough to cover a football pitch with one metre of dry snow.
Besides the fact that many resorts without artificial snow wouldn't be economically viable (costing adjacent businesses jobs), we must acknowledge that snow production's environmental impact is minimal.
First, we must compare appropriately. Multiplying 1 litre of milk or petrol by 35,000 seems enormous. But a swimming pool measuring 50x20 metres with 1.5m average depth holds 1,500,000 litres. Compared to rivers or reservoirs... it's not that much water.
But is all this water truly "wasted"? This isn't a linear process where water enters one end and disappears. The same water deposited as snow on mountains returns to reservoirs when melted, being reused in the system. Ultimately, this process keeps water on the mountain longer, eventually reaching rivers post-season.
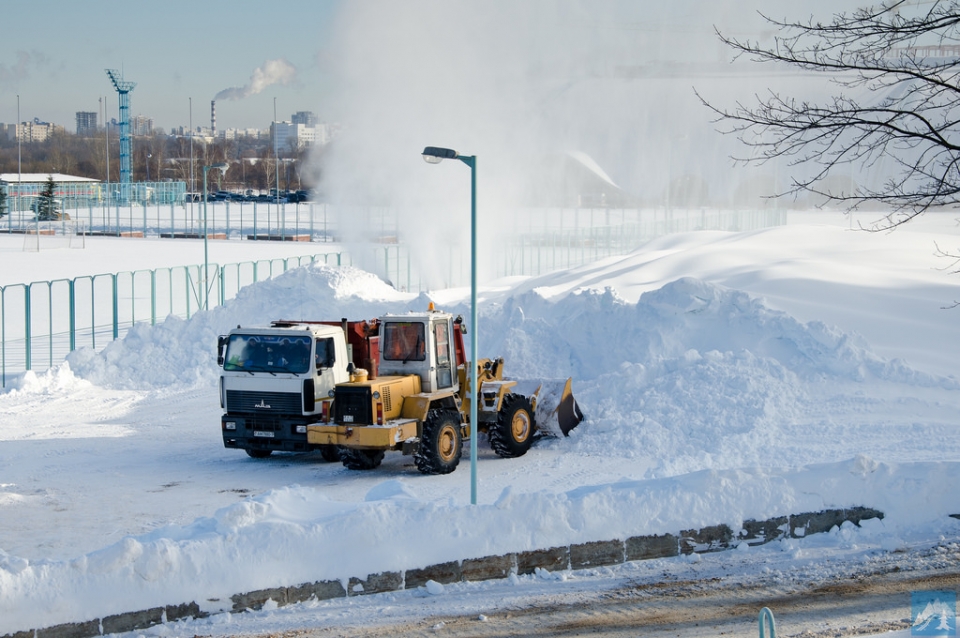
A small portion does get "lost" - some evaporates or sublimates, returning to the atmosphere. Moreover, a single half-metre snowfall (quite common) deposits as much water as a resort might use all year.
In conclusion, artificial snow isn't environmentally harmful, and opposition often stems from misinformation or political agendas.